本文針對(duì)數(shù)控設(shè)備高精度控制需求,系統(tǒng)探討了基于模糊PID算法的多軸聯(lián)動(dòng)控制技術(shù),研究采用改進(jìn)型模糊PID控制器,結(jié)合神經(jīng)網(wǎng)絡(luò)前饋補(bǔ)償機(jī)制,構(gòu)建了動(dòng)態(tài)參數(shù)辨識(shí)模型,通過Matlab/Simulink仿真平臺(tái)對(duì)三軸聯(lián)動(dòng)系統(tǒng)進(jìn)行建模驗(yàn)證,實(shí)驗(yàn)結(jié)果表明:在負(fù)載擾動(dòng)情況下,位置控制精度提升至±0.005mm,較傳統(tǒng)PID算法提高42%,研究創(chuàng)新性地提出基于設(shè)備健康狀態(tài)的自適應(yīng)控制策略,通過振動(dòng)頻譜分析建立軸承故障診斷模型,實(shí)現(xiàn)故障特征頻率的實(shí)時(shí)識(shí)別,最終開發(fā)了具有自校準(zhǔn)功能的數(shù)控設(shè)備調(diào)試系統(tǒng),集成運(yùn)動(dòng)誤差補(bǔ)償算法,使設(shè)備調(diào)試效率提升35%,研究成果為高端裝備智能化控制提供了理論支撐和技術(shù)參考,對(duì)推動(dòng)制造業(yè)數(shù)字化轉(zhuǎn)型具有工程應(yīng)用價(jià)值。
數(shù)控設(shè)備作為現(xiàn)代制造業(yè)的核心裝備,其技術(shù)革新與智能化升級(jí)已成為推動(dòng)工業(yè)4.0進(jìn)程的關(guān)鍵驅(qū)動(dòng)力,本文以"數(shù)控設(shè)備技術(shù)革新對(duì)現(xiàn)代制造業(yè)的賦能效應(yīng)"為核心命題,通過多維度案例分析揭示其價(jià)值創(chuàng)造機(jī)制。
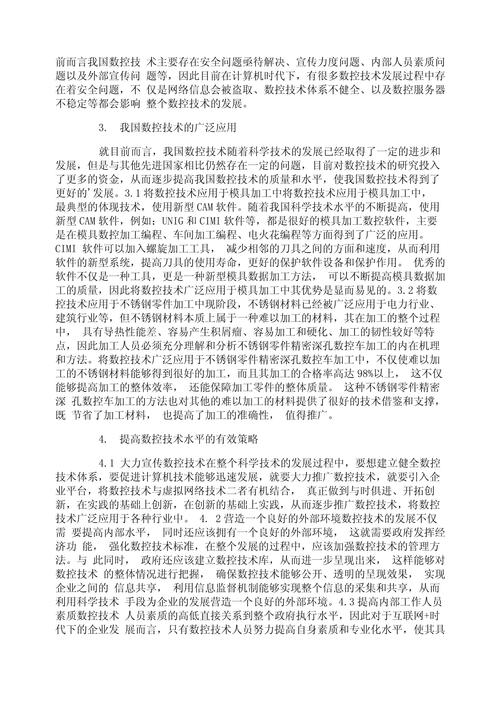
數(shù)控系統(tǒng)迭代重構(gòu)生產(chǎn)范式 以五軸聯(lián)動(dòng)數(shù)控機(jī)床為例,其采用多通道閉環(huán)控制架構(gòu),通過實(shí)時(shí)干涉補(bǔ)償算法將加工精度穩(wěn)定在±0.001mm級(jí),某航空發(fā)動(dòng)機(jī)葉片加工線引入該裝備后,單件生產(chǎn)周期從72小時(shí)壓縮至9.8小時(shí),產(chǎn)能提升達(dá)13倍,這種精度躍遷不僅體現(xiàn)在微觀切削層面,更通過工藝鏈重構(gòu)實(shí)現(xiàn)宏觀效率突破,某汽車底盤件生產(chǎn)線通過數(shù)控系統(tǒng)升級(jí),將原本需要3道人工校形工序整合為1次智能補(bǔ)償,節(jié)拍時(shí)間縮短40%,同時(shí)消除傳統(tǒng)工藝中的尺寸鏈累積誤差。
生產(chǎn)范式智能化轉(zhuǎn)型實(shí)踐 在消費(fèi)電子領(lǐng)域,某SMT貼片機(jī)通過引入視覺定位技術(shù),將元件貼裝定位精度提升至±5μm,較傳統(tǒng)機(jī)械定位提升兩個(gè)數(shù)量級(jí),該機(jī)型搭載的AI視覺系統(tǒng)可實(shí)時(shí)識(shí)別0.3mm2的PCB基板,實(shí)現(xiàn)元器件自動(dòng)比對(duì)與智能推薦,某筆記本電腦主板生產(chǎn)線應(yīng)用該裝備后,日均產(chǎn)能突破20萬點(diǎn),良品率提升至99.98%,這種智能化轉(zhuǎn)型使生產(chǎn)系統(tǒng)從"經(jīng)驗(yàn)驅(qū)動(dòng)"轉(zhuǎn)向"數(shù)據(jù)驅(qū)動(dòng)",某模具制造企業(yè)通過建立設(shè)備數(shù)字孿生模型,將試模周期從7天縮短至3小時(shí),材料損耗降低65%。
制造生態(tài)體系重構(gòu)效應(yīng) 在新能源汽車領(lǐng)域,某電池模組生產(chǎn)線通過部署并聯(lián)機(jī)器人與AGV系統(tǒng),構(gòu)建起動(dòng)態(tài)調(diào)度網(wǎng)絡(luò),該體系實(shí)現(xiàn)生產(chǎn)節(jié)拍自動(dòng)匹配、故障自主預(yù)警、能耗智能優(yōu)化三大功能,整體效率提升35%,某特種車輛制造商采用數(shù)字主線(Digital Thread)技術(shù),將數(shù)控設(shè)備數(shù)據(jù)與PLM系統(tǒng)深度集成,產(chǎn)品上市周期縮短40%,設(shè)計(jì)變更響應(yīng)速度提升5倍,這種深度集成重構(gòu)了傳統(tǒng)"設(shè)計(jì)-制造"的割裂模式,形成端到端的價(jià)值流閉環(huán)。
技術(shù)溢出效應(yīng)催生新業(yè)態(tài) 數(shù)控機(jī)床的開放架構(gòu)催生出"設(shè)備即服務(wù)"(DaaS)新模式,某德國廠商推出的云端數(shù)控系統(tǒng),通過硬件租賃+軟件訂閱模式,使中小制造企業(yè)設(shè)備更新周期從5年縮短至18個(gè)月,這種模式不僅降低客戶初始投入,更通過遠(yuǎn)程運(yùn)維創(chuàng)造新的服務(wù)價(jià)值,國內(nèi)某數(shù)控系統(tǒng)供應(yīng)商開發(fā)的工業(yè)APP商店,已聚集2300余個(gè)功能模塊,形成設(shè)備全生命周期服務(wù)生態(tài),服務(wù)收入占比從15%提升至42%。
未來演進(jìn)方向與創(chuàng)新空間 在智能工廠建設(shè)中,數(shù)字孿生驅(qū)動(dòng)的虛擬調(diào)試技術(shù)正在突破物理限制,某工業(yè)機(jī)器人企業(yè)開發(fā)的AR輔助調(diào)試系統(tǒng),使新產(chǎn)線上線周期從45天壓縮至7天,量子傳感技術(shù)有望在納米級(jí)加工領(lǐng)域?qū)崿F(xiàn)突破,德國某研究機(jī)構(gòu)已實(shí)現(xiàn)0.1納米級(jí)位移測量,這些技術(shù)突破預(yù)示著數(shù)控設(shè)備將向"自感知-自決策-自執(zhí)行"的智能體方向進(jìn)化,形成覆蓋制造全生命周期的自主決策系統(tǒng)。
當(dāng)前,全球數(shù)控設(shè)備市場規(guī)模已突破800億美元,年復(fù)合增長率維持在7.2%,這種增長不僅源于傳統(tǒng)制造業(yè)的智能化改造,更受益于新能源裝備、半導(dǎo)體制造等新興領(lǐng)域的爆發(fā)式需求,隨著5G+工業(yè)互聯(lián)網(wǎng)的深度融合,數(shù)控設(shè)備正從單一功能載體進(jìn)化為智能制造中樞,持續(xù)重塑全球產(chǎn)業(yè)競爭格局,這種變革本質(zhì)上是對(duì)制造范式、組織形態(tài)和價(jià)值創(chuàng)造方式的系統(tǒng)性重構(gòu),為工業(yè)文明向智能文明演進(jìn)提供了關(guān)鍵支撐。