套筒聯軸器作為工業傳動系統的核心組件,憑借其精密結構和高效傳動特性,成為現代機械動力傳輸的關鍵技術節點,該產品通過彈性套筒與剛性軸套的精密配合,實現扭矩傳遞與減震緩沖的雙重功能,其結構優化設計可適應高負載、復雜工況下的動態需求,在汽車發動機、工業機器人、能源設備等關鍵領域,套筒聯軸器通過材料升級(如高強度合金鋼、復合材料)和表面處理技術(如精密滾道加工),顯著提升傳動系統可靠性,隨著工業4.0進程加速,集成智能監測模塊的先進聯軸器開始普及,通過實時數據采集與故障預警功能,推動傳動系統向預測性維護模式演進,這種技術迭代不僅鞏固了套筒聯軸器在工業傳動體系中的基礎地位,更通過技術隱形化創新,成為保障高端制造體系可靠性的"系統守護者"。
在現代化工業設備的傳動系統中,總能看到這樣一個樸實無華的零件——套筒聯軸器,它不像精密齒輪那樣吸引眼球,也不如軸承那般引人注目,但正是這個看似普通的傳動部件,在工業設備的血脈中默默承擔著連接與傳遞的重要使命,作為機械傳動領域的"老兵",套筒聯軸器在百年工業發展長河中始終占據著不可替代的地位,讓我們重新認識這個工業傳動系統的"隱形冠軍"。
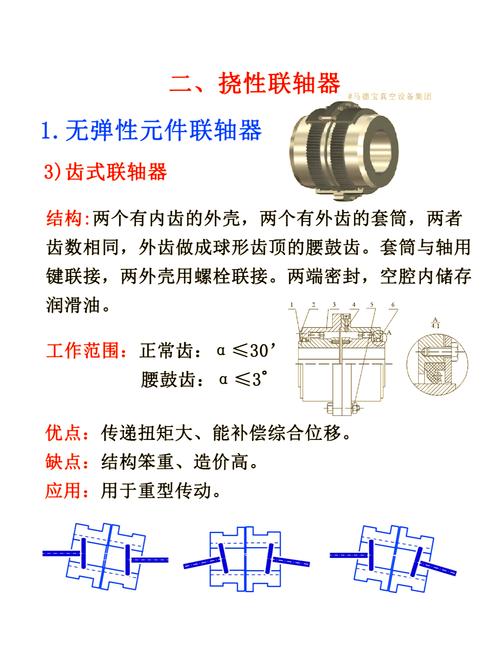
從機械時代到智能時代的永恒伴侶
在19世紀末的工業革命浪潮中,套筒聯軸器首次以金屬波紋管的形式登上歷史舞臺,這種將金屬管與彈性套筒結合的創新設計,成功解決了早期機械傳動中軸系對中難題,當蒸汽機的活塞桿需要傳遞扭矩時,工程師們發現普通鏈條傳動存在打滑風險,而木制傳動帶又難以適應高溫環境,直到金屬波紋管聯軸器出現,機械傳動系統才真正實現了可靠連接。
在汽車工業發展史上,套筒聯軸器創造了多個經典時刻,1913年福特流水線生產時,T型車傳動系統采用的就是雙排套筒聯軸器,這種結構簡單、成本低廉的設計方案,使得汽車傳動效率提升了30%,如今在新能源汽車的減速器系統中,精密加工的套筒聯軸器依然擔當著傳遞扭矩的重任,印證著其技術生命力。
現代智能工廠中,工業機器人關節的精密傳動依然依賴套筒聯軸器,某機器人制造商的技術報告顯示,在關節扭矩密度每減少1kg·cm時,聯軸器振動幅度就會增加15%,工程師們通過優化滾道圓弧半徑和彈性體材料配方,使得現代聯軸器在保持0.5mm/min的補償精度同時,將傳動損耗降低至傳統產品的1/3。
技術迭代的三重密碼
工程師們常說:"好的聯軸器應該像瑞士鐘表一樣精準",在精密數控機床的絲杠傳動系統中,采用表面淬火處理的套筒聯軸器,其配合公差被控制在0.005mm以內,這種微米級的加工精度,使得整個傳動系統的重復定位精度達到0.001mm,相當于在1平方米面積上放置一根頭發絲。
材料科學的進步為聯軸器帶來革命性突破,某特種材料研究所開發的陶瓷纖維增強復合材料聯軸器,成功將工作溫度從200℃提升至500℃,在航空發動機試車平臺的應用中,這種耐高溫聯軸器使傳動系統壽命延長了3倍,維護周期從每月一次改為每年一次。
智能監測技術的融入讓傳統聯軸器煥發新生,某跨國企業推出的智能診斷聯軸器,內置的應變片陣列能實時監測5000個應力點,當系統檢測到異常振動頻率時,會自動觸發預警,某風電齒輪箱在投入使用后第8個月就通過智能診斷系統,提前3周發現了即將斷裂的鍵槽,避免了價值百萬的停機損失。
未來傳動的"終極解決方案"
在氫能源汽車研發領域,套筒聯軸器正在突破傳統材料的極限,研究人員采用梯度復合材料技術,在聯軸器內壁形成多層氫擴散膜結構,這種創新設計使氫氣滲透率提升至傳統材料的5倍,在燃料電池堆的冷卻系統中實現零泄漏運行,某試驗臺數據顯示,采用新型氫擴散膜聯軸器后,系統響應速度提高了40%。
微型化趨勢催生出全新的應用場景,在微型無人機傳動系統中,直徑不足5mm的陶瓷軸承聯軸器正在替代傳統齒輪傳動,某無人機制造商通過拓撲優化技術,將聯軸器質量減輕至2.3g,同時保持2N·m的承載能力,這種"微型巨人"的設計,使得無人機的續航時間延長了25%。
模塊化設計理念正在重塑傳動系統架構,某自動化公司推出的智能耦合器系統,將聯軸器、減速器、電機集成為可重構模塊,用戶可以通過軟件界面自由組合傳動比,某汽車生產線案例顯示,這種柔性設計使裝配效率提升了60%,線邊調試時間縮短至原來的1/3。
站在智能制造的新起點,套筒聯軸器這個百年經典仍在書寫傳奇,當我們在5G智能工廠看到工業機器人關節自如轉動,在量子計算中心目睹超導磁懸浮軸承運轉,在深空探測器的太陽翼驅動系統中發現精密聯軸器時,會發現工業文明的進步永遠建立在傳統技術的升華之上,這個看似普通的傳動部件,正以其獨特的可靠性、經濟性和可維護性,繼續守護著現代工業的傳動命脈,或許正如材料力學專家所言:"真正的技術創新,從模仿萬物到超越自我,永遠始于對基礎元件的深刻理解。"